|
What To Do: |
- Reflow soldering and curing.
- Microwave Hybrids
- Fluxless Gold/Tin Reflow
- Chip Scale Packaging
- BGA
- SMT
- LED Diode Reflow
|
|
- Curing, components and epoxies
- High Density Packaging/Substrates
- Flex Circuits
- Fixtured Assemblies
- High Mass Items
- Wafer Bump Reflow
- Lead Frames
|
|
|
Digital Hot Plate |
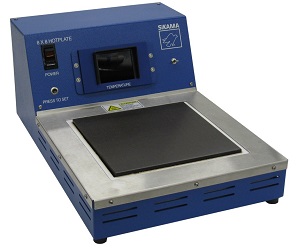 |
|
Let’s begin with the Digital Hot Plate. The Hot Plate incorporates microcomputer circuitry which controls key parameters. The system is very simple to operate, with temperature programmable from room temperature to 350°C in one-degree increments. The temperature is also measured by K-type thermocouple, complete with an easy calibration procedure. Precision machined 8” aluminum plates are used to achieve even temperature and flatness for the most exacting results.
Suggested applications include:
- High mass component processing
- Surface mount component reflow
- Hybrid circuit fabrication and repair
- Temperature cycling of components
- Curing, components and epoxies
- Rework
- Substrate materials such as FR4, aluminum, beryllium, ceramic, copper and silicon are all compatible for conduction heat reflow
|
Falcon 5C |
The Falcon 5C solder reflow oven combines bottom-up conduction and top-down convection technology
with precise calibration of temperature and purity of atmosphere for ultimate control of your
solder or curing process. It is a tabletop system intended for production runs of moderate product
sizes and is manually operated. Maximum substrate size is 5” x 5.75”.
The Falcon 5C is a 7 zone system capable of temperatures up to 400°C featuring a liquid cooled load platform,
four bottom conduction/top convection heat zones, one bottom conduction/top convection liquid cooled zone,
and a liquid cooled offload platform. Each heated zone has independent set point controls and gas flow controls
to ensure consistent and precise temperatures for greater profile flexibility. The internal liquid cooled
zone ensures a process cool down in an inert atmosphere prior to the product exiting onto the offload platform.
Parts are transported through the system using sweeper bars that operate in a “dwell” or timed delay mode.
The system may be operated with air, nitrogen, or forming gas. The inert gas flow enters the reflow chamber
through small orifices in the top heated platens and exits the sides to prevent contamination of adjoining
zones and completely eliminate flux buildup. In addition to heating the inert gas, the top platens also
contribute significant radiant heat to the reflow process and are easily adjusted to minimize the opening
of the reflow chamber, down to as low as 1/4", thus conserving inert gas consumption while maintaining the
desired oxygen level in the chamber. If the need is to process a large high mass assembly the top platens
can easily be raised to accommodate a part that is over 4” tall. Curtains on each end of the chamber will
assist in lowering the O2 ppm when tall parts are processed.
Suggested applications include:
- LED die reflow
- Fluxless gold/tin reflow
- BGA reflow
- BGA reballing
- High mass assemblies
- Curing, components and epoxies
- Substrate materials such as FR4, aluminum, beryllium, ceramic, copper and silicon are all compatible for conduction heat reflow.
|
|
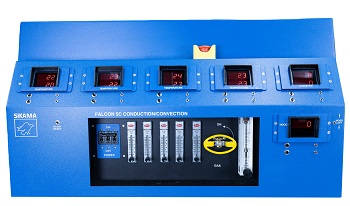 |
|
|
Ultra Profile 2000 |
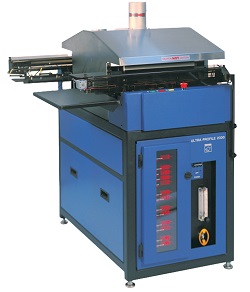 |
|
The patented UP2000 solder reflow oven features state of the art technological
advancements designed to provide ultimate control of your solder reflow process.
The furnace combines bottom-up conduction and convection with top-down convection,
precise calibration of temperature and purity of atmosphere. The system is available
in 2 configurations, either a manually loaded stand-alone unit or an automated version which
utilizes robotics, sensors and SMEMA interface connection to link into a line with other
automated assembly machines.
The UP2000 is a 7 zone system capable of temperatures up to 400°C featuring a liquid-cooled loading
platform, 4 top and bottom conduction + convection heat zones, 1 top and bottom conduction +
convection liquid-cooled zone and a liquid cooled offload platform. Each top and bottom heated
zone has independent set point controls and gas flow controls to ensure consistent and precise temperatures
for greater profile flexibility. The internal liquid-cooled zone ensures a process cool-down
in an inert atmosphere prior to the product exiting onto the offload platform. Parts are transported
through the system using sweeper bars that operate in the “dwell” mode allowing for adjustable cycle
times capable of less than 10 seconds per cycle.
The system may be operated with air, nitrogen or forming gas. The inert gas enters the reflow chamber
through small orifices in the top and bottom heated platens and exits the sides to prevent
contamination of adjoining zones and completely eliminate flux buildup. In addition to the heated
inert gas, the top platens also contribute significant radiant heat to the reflow process and are
easily adjusted to minimize the opening of the reflow chamber to as low as ¼”, thus conserving
inert gas consumption while maintaining the desired oxygen level in the chamber. Maximum substrate
size is 3.9” x 12”.
Suggested applications include:
- BGA strips
- Lead frames
- Die soldering
- LED die reflow
- Flip chip and insulated metal core substrates
- Curing, components and epoxies
- Auer boat carriers
- Substrate materials such as FR4, aluminum, beryllium, ceramic, copper, glass epoxy and silicon are all compatible for conduction heat reflow
- Inline automated processing
|
Ultra Profile 4000 |
Similar to the UP 2000 in format, the UP 4000 does have some significant
differences as well. The UP4000 is a 12 zone system featuring a liquid
cooled loading platform, 7 top and bottom conduction + convection heat
zones, 3 top and bottom conduction + convection liquid cooled zones and
a liquid cooled offload platform. All zones have independent set point
controls and gas flow controls, and like the UP2000 utilizes internal liquid
cooled zones for process cool down in an inert atmosphere. Parts are transported
through the system utilizing sweeper bars that operate in a “dwell” mode. The system
may be operated with air, nitrogen or forming gas. Maximum substrate size is 3.9” x 12”.
Because of the 7 heat to 3 cool zone ratio this is an ideal system for high volume and
high mass part processes.
Suggested applications include:
- BGA strips
- Lead frames
- Die soldering
- LED die reflow
- Flip chip and insulated metal core substrates
- Curing, components and epoxies
- Auer boat carriers
- Substrate materials such as FR4, aluminum, beryllium, ceramic, copper, glass epoxy and silicon are all compatible for conduction heat reflow
- Inline automated processing
|
|
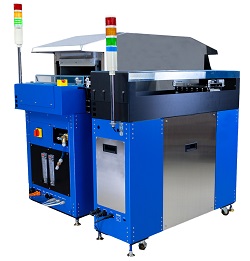 |
|
|
Falcon 8500 |
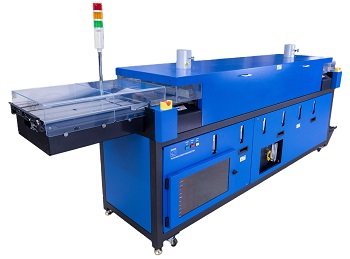 |
|
Incorporating Sikama’s unique “thermal technology” based on
conduction heating in combination with forced thermal
convection, the Falcon 8500 has five heat zones. Each system
includes automatic load and unload buffers with appropriate
sensors providing SMEMA interface connection to link with Sikama ICS 412 Flux coater
or other automated production equipment. Maximum substrate size is 8” x 11.
Prior to entering the heated zones, the temperature of the substrates is stabilized in the
liquid-cooled load zone. Each heated zone has individual set point controls and gas flow
controls that maintain platen temperature to within +/- 2C to ensure consistent and
precise temperatures for reliable, repeatable profiles. The gas is introduced through tiny
perforations in the conduction heating platens and enters the reflow chamber at the
same temperature as the platens. The internal liquid cooled zone ensures a process
cool-down in an inert atmosphere. Further cooling of the substrates is accomplished as
the product exits into the liquid cooled offload zone. The system can be supplied to
operate left-to-right or right-to-left, but direction must be specified when ordering.
The system can be interfaced with a computer, customer supplied, for storing profiles,
monitoring of individual heat zone temperatures as well as dwell time controls and
remote operation. A tray to accommodate a laptop computer is supplied and optional
Windows based software is available. Optional walking beam transportation is also
available.
Suggested Falcon 8500 applications include:
- Wafer bump reflow, 3” to 8” wafers, stand alone or inline with ICS 412 Flux Coater
- LED die reflow
- High mass components and fixtures
- Curing, components and epoxies
- Substrate materials such as FR4, aluminum, beryllium, ceramic, copper, glass epoxy and silicon are all compatible for conduction heat reflow
|
Falcon 1200 |
The Falcon 1200 is a multi-purpose furnace capable of
temperatures up to 400°C that can be used as a reflow
solder system as well as for epoxy curing applications.
Utilizing conduction heating as well as forced thermal
convection, the Falcon 1200 contains 1 load zone, 7 heat
zones and 2 cooling zones and includes automatic load and unload buffers with
appropriate sensors providing SMEMA interface connection to link with the Falcon ICS
412 Flux Coater and automated production lines. The system may be operated air,
nitrogen, or forming gas.
Prior to entering the heated zones, the temperature of the substrate is stabilized in the
liquid-cooled load zone. Each heated zone has individual set point controls and gas flow
controls that maintain platen temperature to within +/- 2C. The gas is introduced into the
reflow chamber through tiny perforations in the conduction heating platens and enters
the chamber at the same temperature set for each zone. The internal liquid cooled zone
ensures a process cool down in an inert atmosphere. Further cooling is accomplished
as the product exits into the liquid cooled offload zone.
Parts are transported through the system in the same manner as other machines,
utilizing sweeper bars that can operate in the “dwell” mode. Optional walking beam
transportation is available at no additional cost. The Falcon 1200 can be interfaced with
a customer-supplied computer using optional Sikama software for storing profiles,
monitoring of individual heat zone temperatures, as well as time controls and remote
operation.
Suggested Falcon 1200 applications include:
- Wafer bump reflow, 3” to 12” wafers, stand alone or inline with ICS 412 FluxCoater
- LED die reflow
- High mass components and fixtures
- Curing, components and epoxies
- Substrate materials such as FR4, aluminum, beryllium, ceramic, copper, glass epoxy and silicon are all compatible for conduction heat reflow
|
|
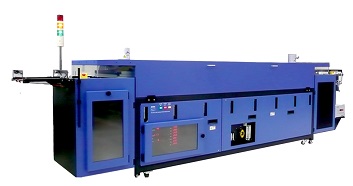 |
|
|
Falcon Ultra Profile1200 (shown with ICS412 Washer) |
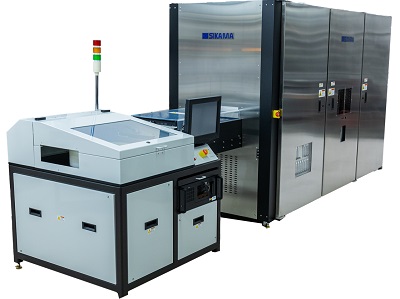 |
|
The UP 1200 is a multi-purpose, continuous flow, reflow
and curing oven capable of temperatures up to 400°C and
atmosphere levels as low as 10ppm O2.
The UP 1200 extends Sikama’s offering of 300mm ovens
with the addition of this bottom conduction, top convection system. With eight (8) work
zones internal to the oven: six (6) heat zones and two (2) cooling zones the oven is
capable of a wide variety of processes.
This versatile oven can be used in solder reflow applications from 300mm 10um wafer
bumping to 5kg microwave power modules as well as for epoxy curing. The ovens
“Walking Beam” transport mechanism is designed to move even the heaviest of these
work items from zone-to-zone through the oven with ease.
Because of the top and bottom heat this oven is capable of producing excellent reflow
on many different types and sizes of work.
Suggested Ultra Profile 1200 applications include:
- Wafer bump reflow, 3” to 12” wafers, inline with ICS 412 Flux Coater
- LED die reflow
- High mass components and fixtures
- Curing, components and epoxies
- Substrate materials such as FR4, aluminum, beryllium, ceramic, copper, glass epoxy and silicon are all compatible for conduction heat reflow
|
Walking Beam Transport System |
Sikama’s optional walking beam transport system is available on the Falcon 8500,
Falcon 1200 and Ultra Profile 1200 Ovens. The round edge design of the beams was
originally intended to minimize backside scratching of wafers and it has been very
successful for that but it has also proven itself effective in moving fixtures and heavier
substrates through the ovens as well. The illustration below shows how the beam
rotates to lift the part off of the platen prior to moving it to the next zone.
|
 |
Falcon ICS 412 Flux Coater |
The Falcon ICS 412 inline flux coating/wafer washing system is capable
of dispensing up to 4 process fluids plus the optional back side rinse (2
standard – i.e. flux, bowl wash) on wafers ranging in size from 4 inches
to 12 inches (300mm). No tool changes are required when changing from
6” through 12” wafer sizes. With an unlimited number of recipe steps, all process
parameters are fully programmable including dispense start, end, sweep, and height.
The servo drive spin chuck is programmable with speeds from 1 to 2000 RPM. The spin
chuck vacuum system includes a fluid trap reservoir to prevent vacuum system
contamination. The fully servo driven controlled inline belt transport requires no
adjustments, no robot teaching or sensor adjustments. The diagnostics mode of the
software allows visual maintenance of all inputs, outputs, servomotors and encoders.
The engineering mode allows direct and immediate process changes in real time.
Password protection allows multiple level operator use.
Options include wafer wash capabilities and the ability to process up to 4 fluids with 2
being standard.
|
|
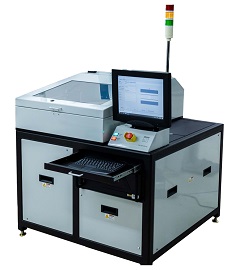 |
|